
We Speak Spanish - Se Habla Español
We offer On-Site Support and / or Virtual Support with a Live Standards Expert
dedicated to your organization at your convenience.


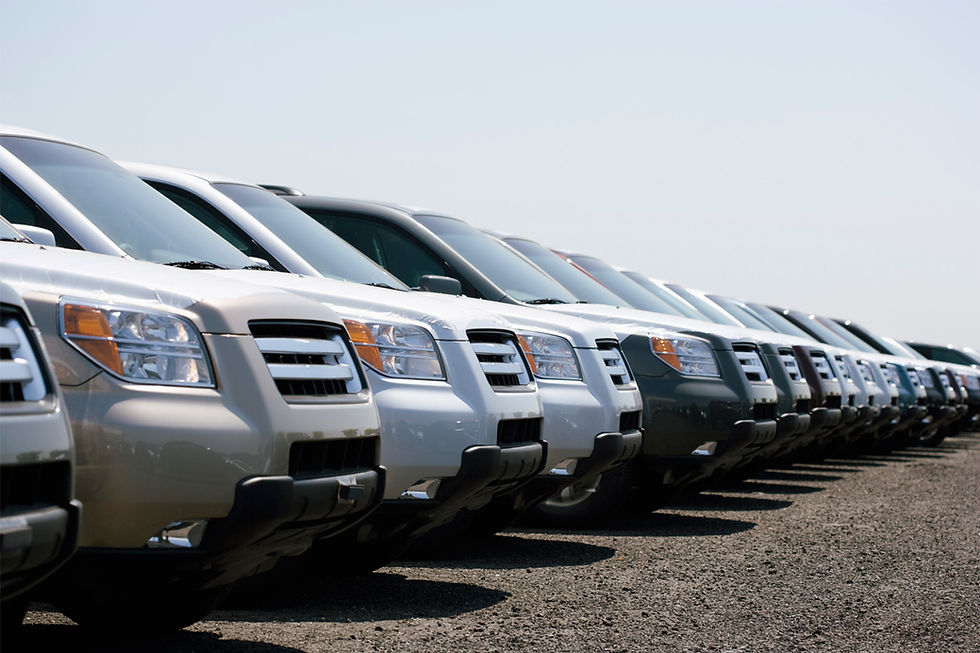
Core Tools
APQP - FMEA - MSA - SPC - PPAP
"The Automotive Quality Core Tools are the building blocks of an effective quality management system. They include Advanced Product Quality Planning & Control Plan (APQP), Production Part Approval Process (PPAP), Failure Mode and Effects Analysis (FMEA), Statistical Process Control (SPC) and Measurement System Analysis (MSA).
Over 30 years ago, AIAG collaborated with the domestic automotive manufacturers to develop common quality methods and tools, which became known as the Quality Core Tools. The tools proved so useful that they were adopted by other manufacturing sectors, including aerospace, defense, medical, and pharmaceutical.
Today, most automotive manufacturers and suppliers require use of one or more of the Core Tools. Therefore, organizations whose employees have mastered the Core Tool processes can assure their customers that the industry’s most qualified individuals are working on their behalf, and that IATF 16949 and applicable quality reference manual requirements will be met without fail."
Source: www.aiag.org
Struggling with Core Tools?
IATF 16949 requires:
8.4.2.3 Supplier quality management system development
The organization shall require their suppliers of automotive products and services to develop, implement, and improve a quality management system certified to ISO 9001, . . . with the ultimate objective of becoming certified to this Automotive QMS Standard.
WCH can help your team and your suppliers understand the value of Core Tools
and use them.

APQP
Advanced Product Quality Planning
APQP is a structured method of determining and implementing the necessary steps to ensure that a product meets the needs of the customer. The objective of APQP is to encourage communication with all interested parties and hold them accountable to complete the required steps in a timely fashion. The effectiveness of APQP is depending on Top Management's commitment to customer satisfaction.

FMEA
Failure Mode Effect Analysis
FMEA is a method for analyzing potential failures. Failure modes are classified by severity of effects, frequency of occurrence, and detect-ability. Current prevention controls are reviewed and new ones may be established to mitigate the possibility of specific failures happening.

MSA
Measurement System Analysis
MSA is a thorough assessment of a measurement process. MSA uses experimental and mathematical tools to determine the variation within the measurement process and understand how the measurement process, itself, contributes to overall process variability.
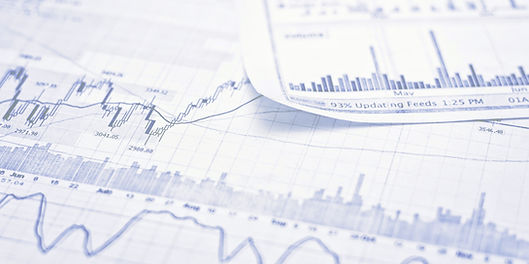
SPC
Statistical Process Control
Process performance is monitored utilizing the appropriate statistical techniques. Process capability and control requirements may be documented in control plans. Capability indices must be achieved and improved throughout production. The goal is to continuously improve by reducing part-to-part variation and eliminating all waste.

PPAP
Production Part Approval Process
PPAP is a standardized process used by the automotive and aerospace industries to help interested parties (i.e. customers, manufacturers and suppliers) communicate and approve production designs and processes before, during, and after manufacture. It is used throughout the product life-cycle to ensure that parts can be consistently and repeatedly produced with the same quality results.